Smart Safety for Automated Thermostat Housing Production Line
A Winning Collaboration between DeD Automation and ReeR Safety
About DeD Automation
DeD Automation is an Italian system integrator specializing in the design and manufacture of special machines for industrial automation. With a strong experience in the most demanding sectors, particularly automotive, the company has established itself as a strategic partner for customers who need systems for the testing, assembly, packaging and testing of small to medium components. DeD’s approach is distinguished by its attention to the customer’s specific needs, starting with listening and preliminary analysis of the object to be automated. Each project is developed in-house: from 3D mechanical design to electrical development, hardware, software and, a central element, functional safety. DeD’s design philosophy is that safety is not a final addition, but an integral part of the initial concept of the system.
DeD’s approach is distinguished by its attention to the customer’s specific needs, starting with listening and preliminary analysis of the object to be automated. Each project is developed in-house: from 3D mechanical design to electrical development, hardware, software and, a central element, functional safety. DeD’s design philosophy is that safety is not a final addition, but an integral part of the initial concept of the system.
The Client and the Challenge
For a major manufacturing company with which it has worked for more than 20 years, operating in the automotive sector and specializing in the manufacture of thermostat housing, DeD designed and commissioned a new advanced automated line in 2022. The client’s goal was to increase production efficiency while maintaining high quality standards and integrating a safety system capable of ensuring operational continuity even in the event of localized interventions.
The main challenge was to create a modern, high-performance line equipped with modular, intelligent safety systems that could handle the complexity of the process without compromising productivity.
The Production Line: Structure and Operation
TThe line developed by DeD stretches about 14 meters and consists of 16 operating stations divided into five functional macro-zones. The production cycle is fully automated, but requires the presence of the operator at two strategic stages: initial loading and final unloading of the good product. The average cycle time for each part is about 35 seconds.
Zone 1 – Initial Loading and Pre-Assembly: The operator manually loads components inside a rotofriction welder. After the gasket is added, the part is placed on a pallet that begins its advancement down the line. The area is protected by an intangible barrier and interlocked movable guards, which allow safe intervention if necessary;
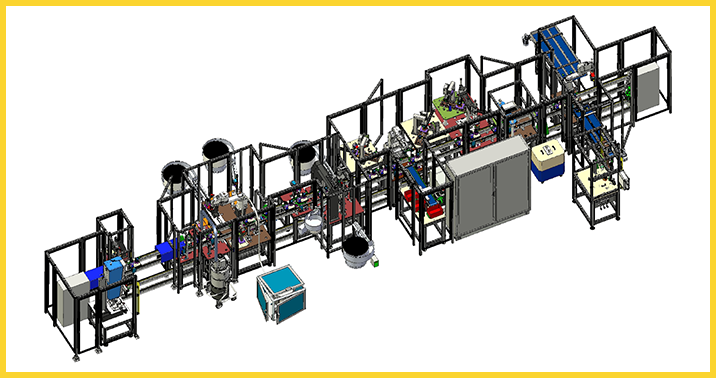
Zone 2 – Automatic Assembly: Here, automatic assembly of various components such as springs, sleepers, bulbs, seals, sensors and forks, fed through vibrators, takes place. Quality control is integrated into the process. Any jamming of a component does not stop the entire line, but only the affected portion, ensuring continuity of the production cycle;
Zone 3 – Testing and Marking: In this phase, pneumatic tightness, electrical tightness, continuity check and leakage check are carried out. Conforming components are laser-marked to ensure traceability;
Zone 4 – Sorting: The system performs automatic sorting between conforming and rejected components, with the possibility of categorizing the reason for rejection (electrical defects, incorrect assembly, testing errors, etc.);
Zone 5 – Final Check and Packing: The operator performs a final check, reads the Data Matrix, verifies the presence of all expected components, and applies protective caps. The products are then ready for shipment.
Each zone is designed to operate independently: in the event of a malfunction or need for maintenance at a specific point, only the affected zone can be stopped, without affecting the entire process. Each of these is served by an AHU (air handling unit) that supplies pneumatic power to the workstations. All local AHUs are managed by a central AHU located in the main switchboard that filters and distributes air at 6 bar constantly.
For the needs expressed by the customer and set out in the next section, it is important to note that each station is protected by the following safety devices:
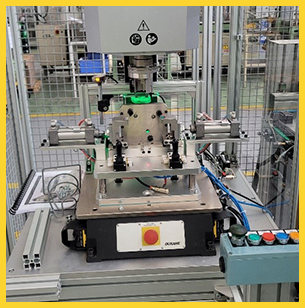
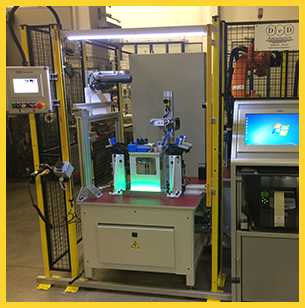
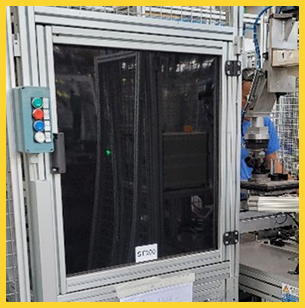
- E-stop: has the purpose of determining machine stop (stop in category 0) and disconnection of pneumatic power. Requires operator intervention to reset;
- Fixed guards: prevent access to moving elements during normal operation and those to which access is occasional for maintenance operations only. They are attached to the machine structure by screws that require the use of tools for disassembly;
- Interlocking movable guards: attached by hinges and provided with handles to facilitate their opening. They are associated with electromagnetic microswitches that prevent them from being opened when the machine is running;
- Safety light curtains: they protect dangerous areas by creating an intangible barrier that is activated when the machining cycle starts and, if intercepted by the operator, immediately stop the moving elements of the machine.
This architecture enables selective and secure management of downtime and recovery operations.
The Safety needs
Due to the complexity and modularity of the line, DeD has precisely defined the safety requirements:
- Independent management of the five zones, without total stops in case of localized interventions;
- Timely control of all safety devices, including emergency pushbuttons, microswitches, interlocks, safety light curtains;
- Intelligent pneumatic and electrical sectioning for each zone, including electrical axis control;
- Future expandability, with safety I/O already prepared for new locations.
- Optimization of wiring and simplification of programming through a centralized safety platform.
Each zone required at least:
- 4 dedicated safety inputs
- Outputs for managing STOs, barriers and guards
- Modules for local signal collection and diagnostics
- Outputs dedicated to managing robots in zones 1 and 2
The ReeR Solution: MOSAIC Modular Safety System
ReeR Safety’s MOSAIC modular platform proved to be the ideal solution to meet the project’s safety needs. At the core of the safety architecture is the MOSAIC M1S COM module, which is equipped with:
- 8 digital inputs
- OSSD outputs (2 pairs)
- 4 test outputs
- 2 RJ45 ports for communication with the main fieldbuses (EtherCAT, PROFINET, Modbus TCP, Ethernet IP)
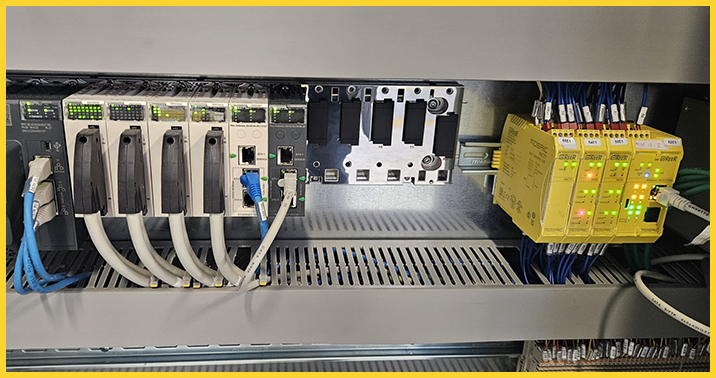
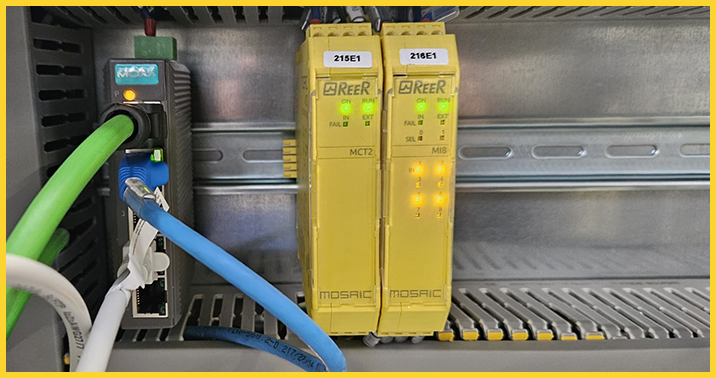
Additional Modules for a Distributed Control
MI16 e MI8: for collecting safety signals (emergency buttons, barriers, interlocks);
MO4: for managing OSSD outputs to actuators, valves or disconnect switches;
MCT1 e MCT2: for remote communication with local boxes via MSC bus.
This configuration allows safe and independent management of each zone. Each local unit communicates with the central module, allowing selective shutdown of individual areas and timely diagnostics. In the event of an intervention, operators can operate safely without compromising the entire line.
ReeR Solution
Safety Controllers and Interfaces
Mosaic is a safety hub able to manage all safety functions of machinery. Configurable and scalable, provides cost reductions and minimal wiring.
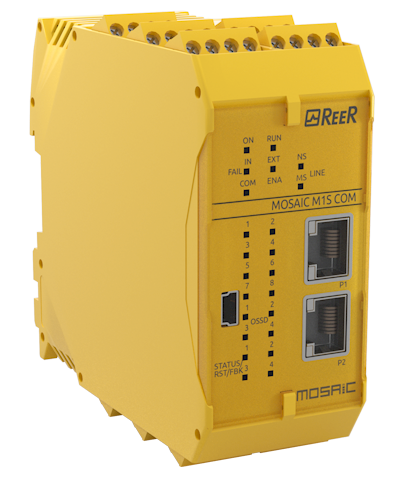
MOSAIC M1S COM
Master Unit for the control of any other expansion unit, can also work as Stand-Alone.
- 8 digital inputs
- 4 inputs for Start/Restart interlock and EDM
- 4 single OSSD safety outputs, or 2 pairs
(PNP 400 mA) - 4 status outputs (PNP 100 mA)
- 4 test outputs (for short-circuits monitoring)
- Integrated field-bus Inteface. Protocols: Ethernet IP, EtherCAT, PROFINET, Modbus TCP
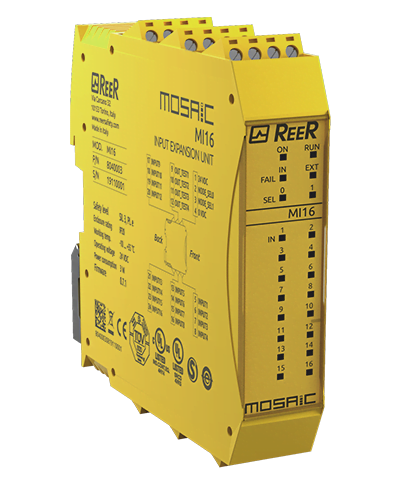
MOSAIC MI8 – MI16
Additional Input unit
- MI8: 8 digital inputs and 4 test outputs
- MI16: 16 digital inputs and 4 test outputs
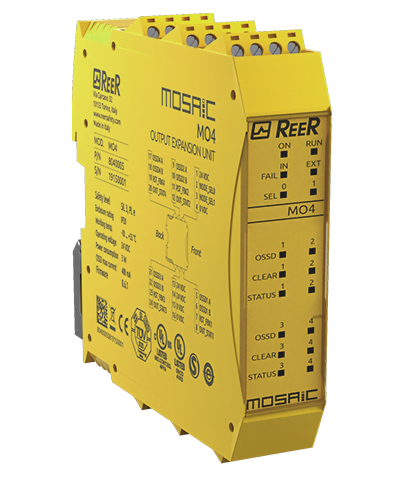
MOSAIC MO4
Output expansion unit
- 4 pairs OSSD safety outputs
- 4 inputs for Start/Restart interlock and EDM
- 4 status outputs
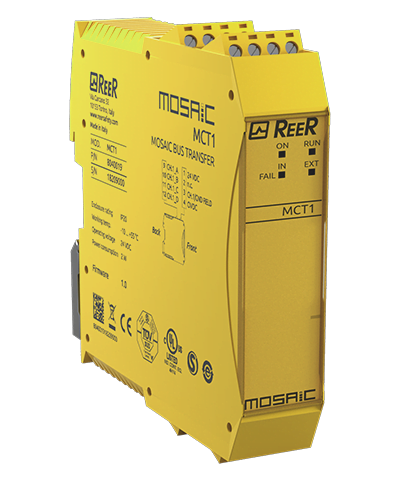
MOSAIC MCT1 – MCT2
Interface unit allowing the connection of remote expansions via MSC bus
- MCT1: 1 connection interface (1 I/O)
- MCT2: 2 connections interface (2 I/O)
Benefits Achieved
The adoption of the MOSAIC platform has brought concrete and measurable benefits:
- Modularity and scalability: ability to easily expand the line with new stations or sensors;
- Reduced wiring and installation time: thanks to the decentralized structure;
- Distributed security management: each zone works autonomously;
- Advanced diagnostics and simplified maintenance with free MSD software, which also enables simulation and design validation;
- High plant availability: downtime is localized and minimized;
- Standardization and simplification: uniformity of components and greater efficiency in spare parts inventory management.
A Solid Partnership for Safe Automation
This project is a virtuous example of how the synergy between an experienced integrator like DeD Automation and a leading provider of safety solutions like ReeR can generate installations that are safe, efficient, and ready for future challenges.
The trust that binds the two companies is the result of years of collaboration and shared success. The MOSAIC system has already been used in numerous applications, from simple counters by choosing it as a stand-alone solution to more complex automated lines such as the one just described for making thermostat housing. Its flexibility and reliability make it the natural choice for any production context that requires uncompromising safety.
If you too are designing an automated line and would like to integrate smart, flexible and scalable safety solutions, contact the ReeR experts.
We are ready to accompany you into a new era of safe automation.
ReeR, your future’s safe!